Kreiss: Mapon ensures reliable temperature monitoring for optimal cargo conditions
Kreiss, a company with headquarters in Riga, Latvia, and offices worldwide from Norway to Kazakhstan, is one of the largest cargo transportation enterprises in Europe. Its fleet includes around 1400 trucks and 1700 refrigerated trailers.
Managing a large fleet presents numerous challenges, from tracking shipments and monitoring temperatures to minimizing human errors. Mapon has had the privilege of partnering with Kreiss for many years, and we’re proud to play a role in their success, ensuring cargo is delivered safely every time.
Mapon helps Kreiss to beat the competition
Once Kreiss started using Mapon temperature monitoring solutions, the company gained a clear competitive advantage and set new standards for refrigerated product shipping companies. Thanks to Mapon solutions, Kreiss also managed to automate many internal processes for reefer unit maintenance and temperature tracking.
Below, we describe the key benefits Kreiss has gained from our fleet monitoring solutions. Read on to discover how these improvements might benefit your fleet as well!
Digital charts instead of paper printouts
These days, clients no longer want to wait for shipments to arrive to see printouts of the reefer unit’s temperature. Instead, clients want to have access to live data to be 100% sure that everything is good with their cargo. Kreiss, being an innovative company, understood that early on. That’s why Kreiss now gives clients tracking links that include easily understandable charts of Carrier reefer unit data:
- the setpoint temperature
- run mode
- return air temperature.
Kreiss clients can check this information on the Mapon platform, available on mobile and desktop, together with plenty of other useful data such as historic routes, real-time location, speed, etc.
Thanks to digital monitoring, Kreiss team members no longer have to analyse large paper printouts to find shipment issues. All data is displayed in a chart and can be easily overviewed.
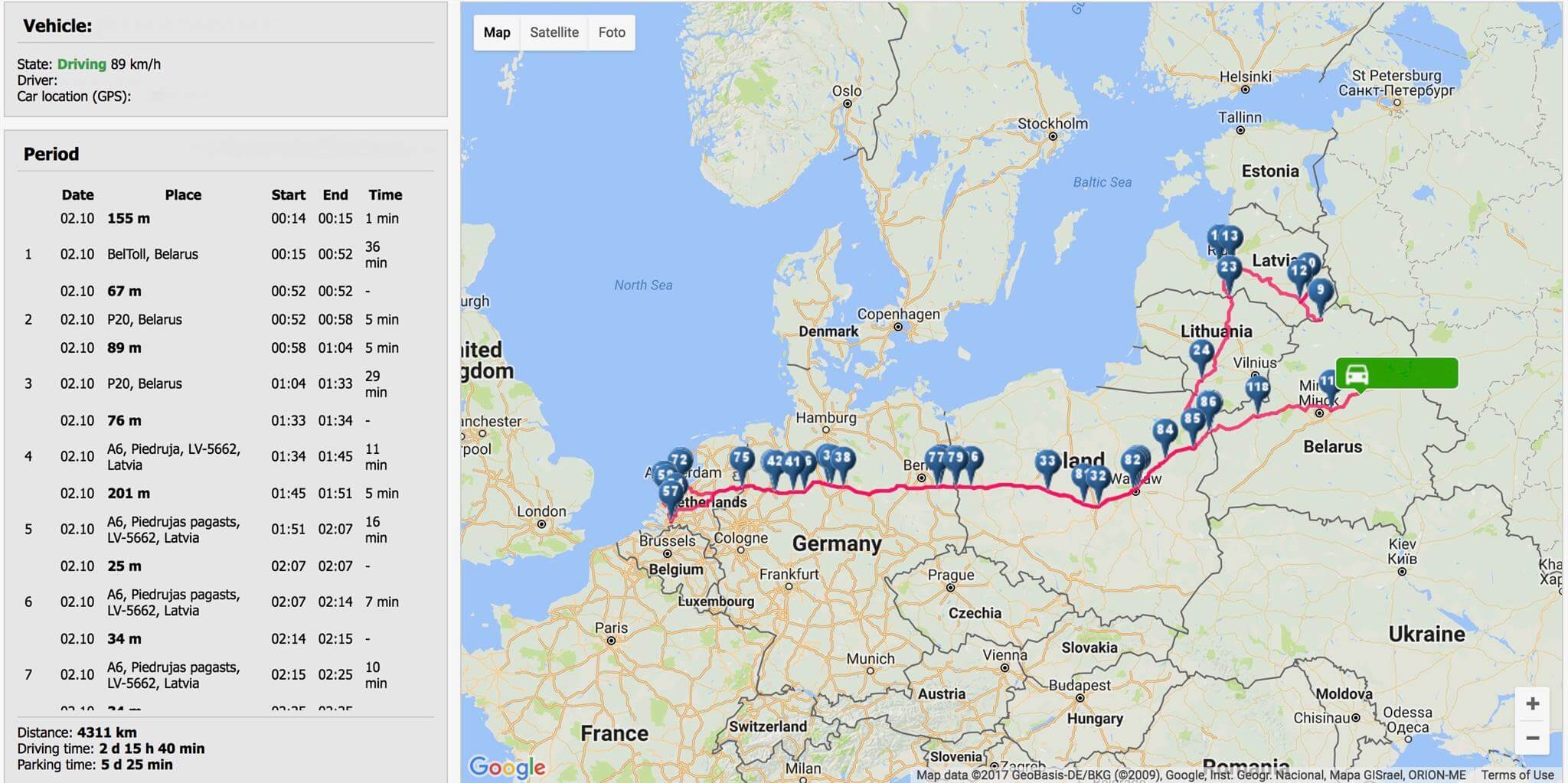
No more human errors in temperature settings
Once Kreiss set up the temperature monitoring solution, the company tackled a large number of human error issues on the road. Some of the most widespread issues were:
- mistaking positive numbers with negative ones (instead of operating at +6°C, the reefer is being operated at -6°C)
- missing or adding an excess decimal point (instead of operating at +6°C, the reefer is being operated at 0.6°C)
Simple mistakes like these can seriously damage the shipment and bring unexpected costs. That’s why temperature monitoring is essential for any company that carries temperature-sensitive products like Kreiss.
Mapon helps fix reefer errors
Kreiss has taken problem-solving to the next level by addressing reefer error conditions on the go. This approach not only minimises the impact of human errors but also enables drivers to handle simple repairs themselves.
With technicians in the office having real-time access to reefer data, they can guide drivers step by step, making quick fixes possible and keeping operations running smoothly.
Here is how this system works at Kreiss: once a reefer unit emits an alert code, it goes directly to the Kreiss internal maintenance planning system, and their reefer technicians decide how to react. Either schedule a maintenance operation in their planning system or contact the driver to resolve the issues immediately.
The Mapon platform also provides information about the nearest Carrier and Thermo King service centres, which is very handy in urgent matters.
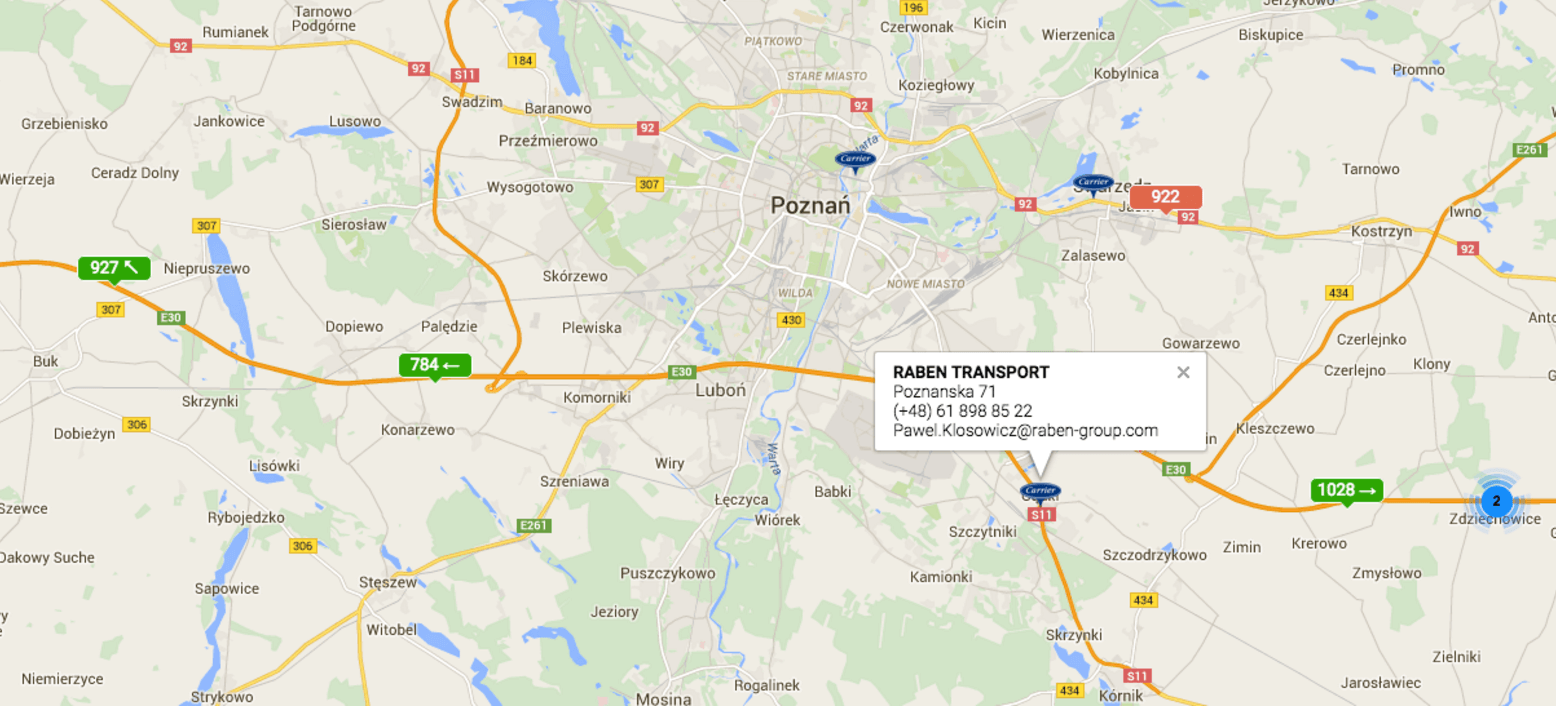
Accurate temperature tracking for every shipment
Kreiss has an internal shipment planning and dispatching system, where they can set up the required reefer parameters for each shipment. This data is sent to the Mapon platform and turned into time-bound alerts. If the temperature or run mode in the time-bound slot is not within the specified range, an alert is generated and sent back to the Kreiss shipment management system. This solution allows for complete automation in terms of temperature monitoring.
Additionally, Mapon has an option to use the alert system to cool down cargo. There are cases when the cargo should be shipped at +4°C, but it is not cooled to that temperature at the loading point. If the driver sets a setpoint of +4°C and the actual cargo temperature is around +15°C, the reefer will rapidly cool the compartment to a temperature below 0°C to reach the desired setting quickly.
However, this rapid cooling process could potentially damage the cargo. Thanks to Mapon, Kreiss found the solution to such challenging situations. The Mapon temperature monitoring solution has a built-in mechanism that alerts the driver when to lower the temperature gradually to cool down the cargo without damaging it.
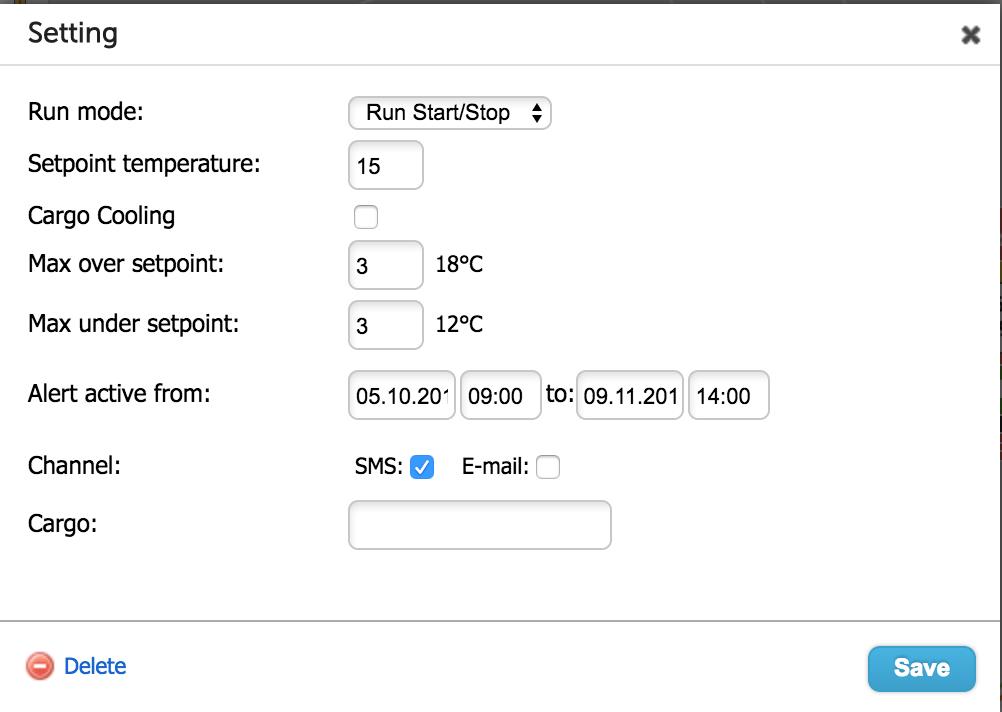
Looking for accurate temperature monitoring for your fleet?
At Mapon, we’ve supported Kreiss and countless other businesses worldwide in building dependable fleet monitoring systems. No matter your industry, our team is ready to create a personalised solution that fits your unique needs.
Contact our team and let us take your operations to the next level!
article updated in 2025